Einsparmöglichkeiten bei Strom und Diesel im Milchkuhbetrieb
In den heute gängigen Haltungssystemen für Milchkühe und deren Nachzucht kann in der Regel auf Heizung oder Zwangsbelüftung verzichtet werden. Daher ist der Energieeinsatz bezüglich der Haltungsverfahren in der Milchrinderhaltung im Verhältnis zu anderen Tierproduktionszweigen relativ gering. Für Stromlieferanten zählen selbst größere landwirtschaftliche Betriebe eher zu den kleinen Abnehmern. Im landwirtschaftlichen Betrieb müssen für Strom unterm Strich ca. 20 ct je kWh und je Liter Diesel knapp 1,50 € gezahlt werden, abzüglich Dieselrückvergütung verbleiben etwa 1,28 € je Liter. Über die letzten Jahre gesehen ist ein kontinuierlicher Anstieg der Energiekosten zu verzeichnen, wie die Grafiken in den Abbildungen 1 und 2 zeigen.
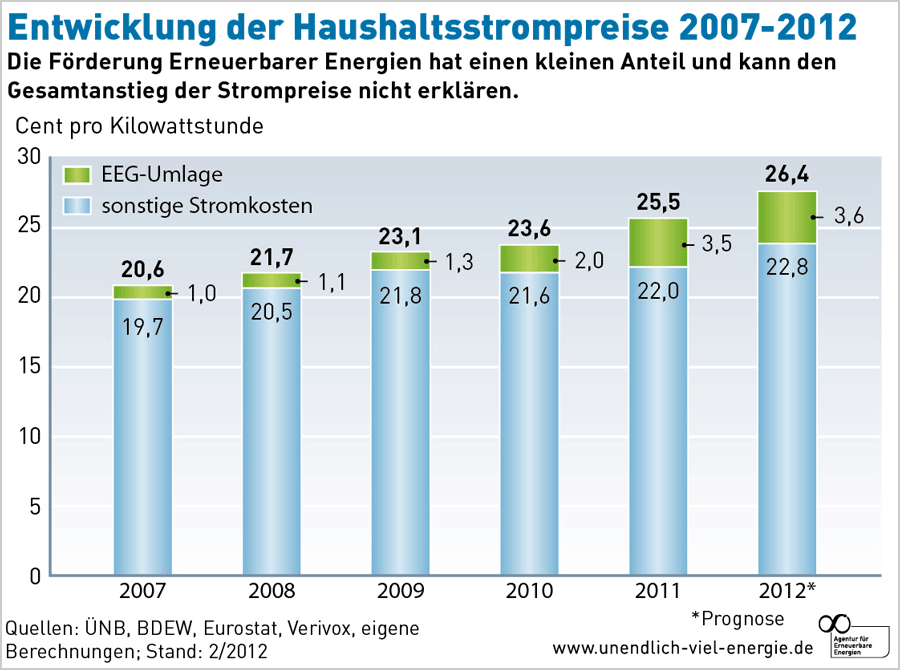
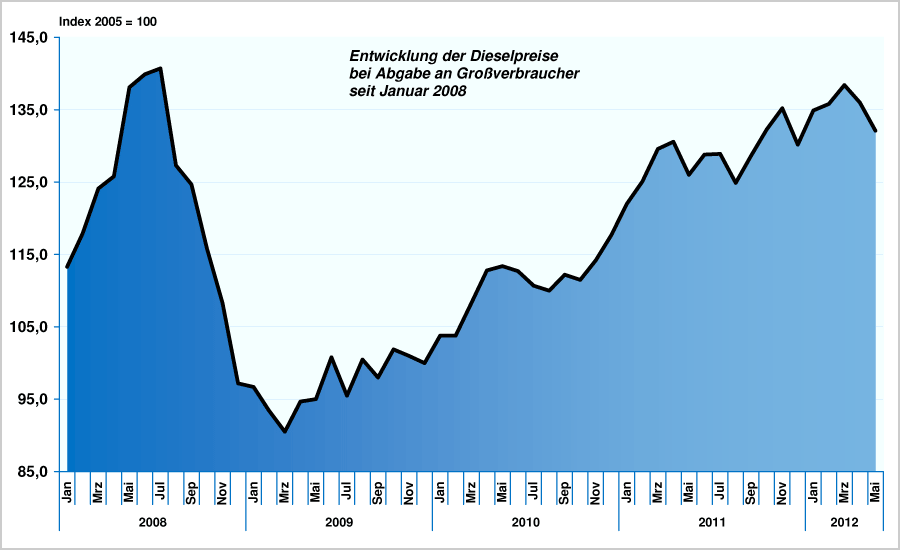
Auch die Einkaufspreise landwirtschaftlicher Betriebsmittel sind von 2009 bis 2011 um 10 % angezogen. Der Preis für fossile Energieträger wird weiterhin steigen und somit die Energiekosten, auch die Strompreise, beeinflussen.
Im Milchkuhbetrieb belaufen sich die Kosten für Wasser, Heizung, Strom, Treib- und Schmierstoffe immerhin auf rund 1,75 ct je kg Milch bzw. ca. 150 € je Kuh und Jahr (BZA 2010/2011). Vor diesem Hintergrund ist es sinnvoll, sich mit Einsparmöglichkeiten zu befassen, wobei die betrieblichen Verbrauche und Kosten enorm unterschiedlich sind.
Tendenziell haben kleinere Betriebe je Produktionseinheit einen geringeren Stromverbrauch als größere Betriebe, was z.B. mit einem höheren Automatisierungsgrad in Großbetrieben zusammenhängen kann. Für Betriebe mit rund 100 Milchkühen wird der Stromverbrauch für eine Milchkuh mit 400 kWh pro Jahr bzw. mit 5 kWh je 100 Liter Milch angegeben. Der größte Anteil entfällt mit etwa 60 % auf die Milchgewinnung. Weitere Punkte sind mit 35 % die Fütterung sowie mit 5 % Beleuchtung und Entmistung (siehe Abbildung 3).
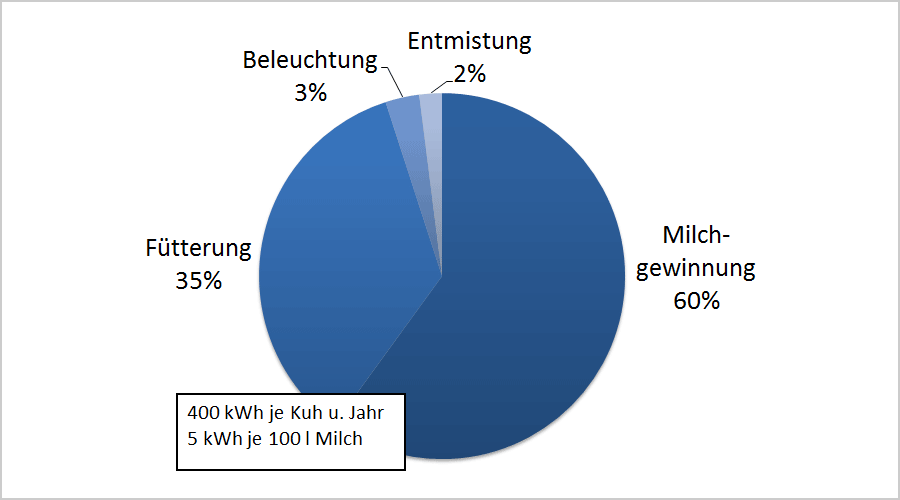
Die Außenwirtschaft nicht berücksichtigt, gibt es im System Milchproduktion verschiedene Ansatzpunkte für Energieeinsparungen, die jeder Betrieb für sich prüfen und optimieren kann. Einige Punkte sollen im Folgenden beispielhaft vorgestellt werden und Anregungen für den eigenen Betrieb geben.
Ansatzpunkte für Energieeinsparungen bei der Futtervorlage in der Rinderhaltung:
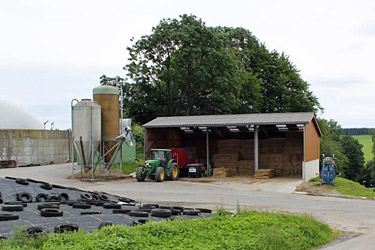

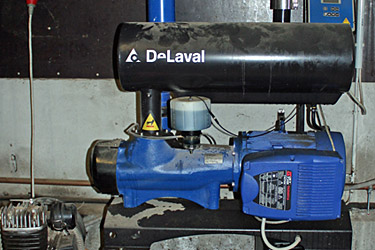

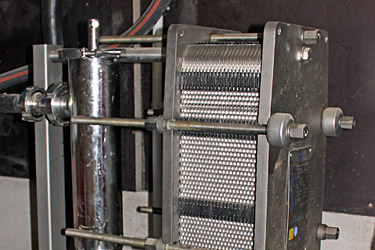

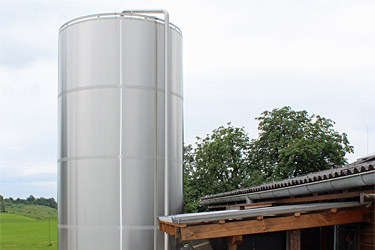

Eine Kraftfutterstation ist in der Regel 24 Std. in Betrieb. Pro 100 W elektrischem Leistungsbedarf der Computerfütterung werden etwa 880 kWh pro Jahr verbraucht. Je nach Betriebssituation kann es sinnvoll sein, Kraftfutter individuell leistungsbezogen zu verabreichen und so Tiergesundheit und die Effizienz der Milchproduktion zu steigern. Bei der Vorlage von Grobfutter, Mischrationen und Totalmischrationen gilt der Grundsatz: Energie sparen beim Füttern = Zeit einsparen! Es geht also darum die Laufzeiten zu minimieren. Hierzu sind bei der Planung folgende Punkte zu beachten:
- optimale Anordnung der Futterachsen
- günstige Zuordnung Lager - Stall
- befestigte Lagerflächen und Transportwege, kurze Wege
- ausreichend Wendeplatz
- Futtertisch durchfahrbar und ausreichend breit
- Entnahme vorbereiten
- Wartung von Maschinen, besonders Messer
- Anzahl der Komponenten und Rationen optimieren
- Auswahl der Komponenten, besonders Partikellänge
- Auswahl der Fütterungstechnik
- mechanische Fördertechnik bevorzugen, pneumatische Geräte haben einen höheren spezifischen Stromverbrauch
Einsparmöglichkeiten bei Güllerühren & -Pumpen - Schlepper- oder Elektroantrieb?
Je nach den betrieblichen Gegebenheiten und Voraussetzungen kann das Handling der Gülle auf unterschiedliche Weise, entweder mit Strom oder mit Diesel angetrieben, geschehen. Die folgenden Beispiele zeigen, dass hierbei Strom betriebene Varianten rein vom Energieverbrauch und somit auch den Energiekosten her vorteilhaft sein können. Sicherlich müssen Gesamtinvestition berücksichtigt und alternative Einsatzmöglichkeiten betriebsindividuell geprüft werden. Der Antrieb per Strom schneidet beim Güllerühren und -Pumpen günstiger ab, da mit hohem Wirkungsgrad gearbeitet wird. Die Verluste z.B. in Form von Wärme sind bereits an anderer Stelle zu verzeichnen und dem Kraftwerk zu verbuchen. Der Wirkungsgrad von Dieselmotoren zum Antrieb von Mixern oder Pumpen ist deutlich schlechter.
Beispiel: Güllerühren im Güllekanal
- Elektromixer (Feste Installation)
- 10 kW Anschlusswert (abh. v. Gülle, baul. Gegebenheiten, usw.)
- 15 min / Tag
= 900 kWh / Jahr
= 180 € / Jahr
- Rührwerk mit Schlepperantrieb
- 80 kW Schlepper (150 g Diesel / kWh = 12 l / h)
- alle 4 – 6 Wochen (10 x 1,5 h / Jahr)
= 180 l Diesel / Jahr
= 225 € / Jahr
Annahmen: Strompreis 0,20 € / kWh, Dieselpreis abzgl. Dieselrückvergütung
1,25 € / l
ohne Arbeitslohn und Gerätekosten (Quelle: LWK NS, Alfons Fübbeker)
Tabelle 1: Gülle pumpen von Stall in Hochbehälter, Beispiel
Pumpenantrieb | ||
---|---|---|
mit Strom | mit Schlepper (150 g Diesel / kWh) |
|
Güllemenge/Jahr | 2000 m³ | 2000 m³ |
Antrieb Pumpe | 11 kW | 60 kW |
Förderleistung | 150 m³/h | 300 m³/h |
Zeitaufwand | 14 h | 7 h |
Energieverbrauch | 154 kWh | 63 l |
Kosten | 31 €/a | 79 €/a |
Annahmen: Strompreis 0,20 € / kWh, Dieselpreis abzgl. Dieselrückvergütung
1,25 € / l
ohne Arbeitslohn und Gerätekosten (Quelle: LWK NRW, Dr. Horst
Cielejewski)
Einsparmöglichkeiten bei der Milchgewinnung und -Lagerung:
Für bestimmte Stromabnehmer rund um die Milchgewinnung gibt Rob Jacobs, Energieberater aus den Niederlanden, folgende Kosten je 100 Liter Milch an:
- Milchkühlung ohne Vorkühlung: 0,20 bis 0,30 €
- Vakuumpumpe bei konventionellem Melken: 0,04 bis 0,30 €
- Warmwasserversorgung: 0,05 bis 0,20 €
- Brunnenwasser (pumpen und reinigen): 0,07 bis 0,20 €
Die Zahlen verdeutlichen auch hier die enormen Spannweiten zwischen den verschiedenen Verfahren und Betrieben.
Für unterschiedliche Melkverfahren können für einen Betrieb mit rund 100 Kühen die in Tabelle 2 dargestellten Anschlusswerte verglichen werden. Das Beispiel zeigt für diese Struktur die Vorteilhaftigkeit für das Verfahren Zirkulationsreinigung + Milchvorkühlung + Direktverdampfungskühlung.
Tabelle 2: Anschlusswerte für verschiedene Melkverfahren am Beispiel eines 100 Kuh Betriebes und Vergleich kalkulierter Energiewerte zum Verfahren 1. (Quelle: Arbeitsgemeinschaft für Elektrizitätsanwendung in der Landwirtschaft e.V. AEL)
Anzahl Kühe | 100 | ||||
kg Quote | 700.000 | ||||
Stromverbrauch (kWh / a) | 35.000 | ||||
Melken und | Vergleich zu Verfahren 1 |
||||
---|---|---|---|---|---|
1 | Zirk.Reinigung + Direktverdampf.-Kühlung | 20 - 25 kW | kW | kWh / a | |
2 | Kochendwasserreinigung + Direktverdampf.-Kühlung | 15 - 18 kW | -6 | 0 | |
3 | Zirk.Reinigung + Eiswasser-Kühlung | 18 - 23 kW | -3 | 2.100 | |
4 | Kochendwasserreinigung + Eiswasser-Kühlung | 10 - 15 kW | -10 | 2.100 | |
5 | Zirk.Reinigung + Milchvorkühlung + Direktverdampf.-Kühlung | 18 - 23 kW | -2 | -8.400 |
Auch beim Melkvorgang selbst kann Strom eingespart werden, indem die Abläufe zügig durchgeführt werden und Routinearbeitszeit minimiert wird. Ähnlich dem Füttern heißt es: Energie sparen beim Melken = Zeit einsparen! Dafür sollten neben anderem folgende Punkte rund um die Melkzeit überprüft werden:
- ruhiger Umgang mit den Tieren
- saubere Euter, dafür sind gutes Liegeboxen- & Laufgangmanagement Vorraussetzung
- gute Eutergesundheit und Melkbarkeit der Herde, eventuell Einteilung in Gruppen
- optimierte Triebwege: trittsicher, gut einzusehen, ≥ 2,5 m breit, eben, gerade, hell, gleiche Farben, keine Hindernisse
- optimierte Bereiche Vorwarten: 1,8 m² / Tier und Nachwarten: 2,5 m² / Tier
- eventuell Einsatz einer automatischen Nachtreibehilfe
- Schnellaustrieb evtl. sinnvoll wenn bereits andere Bereiche optimiert sind
- Eingliederung von Färsen schon vor der Kalbung zu den Kühen
- keine Nebenarbeiten
Zum Melkvorgang und der anschließenden Melkzeug- und Melkanlagenreinigung gehört die Erzeugung eines Vakuums mittels Vakuumpumpe. Bei der Planung eines zum Betrieb passenden Melkstandes sollte auf eine angemessene Dimensionierung von Milchleitung und Vakuumpumpe geachtet werden, um die Größe der Vakuumpumpe begrenzen zu können. Für den Fall, dass sehr lange Melkzeiten im Betrieb anstehen oder eine Ersatzinvestition in dem Bereich getätigt werden soll, kann es sich lohnen eine frequenzgesteuerte Vakuumpumpe anzuschaffen. Frequenzsteuerungen regeln die Vakuumleistung nach dem Milchstrom. Die volle Vakuumleistung wird beim normalen Melkvorgang in der Regel nicht benötigt, so dass geringere und somit energiesparende Drehzahlen völlig ausreichen. Positive Effekte einer Drehzahlsteuerung sind neben der Einsparung der Energiekosten, eine Lärmreduktion und geringere Beanspruchung der Pumpe. Erst beim Spülvorgang wird die maximale Leistung abgerufen. Die Berechnungen in Tabelle 3 geben einen Überblick über die Kosten einer konventionellen sowie einer frequenzgesteuerten Vakuumpumpe bei unterschiedlichen Melkzeiten pro Tag und zeigen deutlich die Vorteile der Frequenzsteuerung. Beträgt die Melkdauer unter 3 Stunden je Tag, ist die Investition zu überdenken.
Tabelle 3: Kostenvergleich und Strombedarf von Vakuumpumpen. (Quelle: Dr. Horst Cielejewski, LWK NRW, verändert nach Fübbeker, LWK NS)
Konventionelle Vakuumpumpe 2000 l/min, 5,5 kW |
Frequenzgesteuerte Vakuumpumpe 2000 l/min, 5,5 kW |
||||
---|---|---|---|---|---|
Anschaffungskosten | € | 4.000 | 6.500 | ||
Tägliche Melkdauer | h | 3 | 6 | 3 | 6 |
feste KostenWartung, Reparatur | € | 640 | 800 | 1.040 | 1.300 |
Strombedarf/ Jahr | kWh | 6.000 | 12.000 | 3.600 | 7.200 |
Stromkosten/ Jahr | € | 1.200 | 2.400 | 720 | 1.440 |
Gesamtkosten/ Jahr | € | 1.840 | 3.200 | 1.760 | 2.740 |
Annahmen: 40 % Ersparnis durch Drehzahlregelung, Strompreis: 0,20 €/kWh
Eine andere Möglichkeit zur Energieeinsparung bei der Vakuumerzeugung ist der Einsatz von zwei Vakuumpumpen, wobei die zweite nur für den vakuumintensiven Spülvorgang in Benutzung genommen wird. Egal welche Variante genutzt wird, Grundvoraussetzung für eine effiziente Funktion ist eine regelmäßige Wartung der Pumpen.
Bei der Melkzeug- und Melkstandreinigung sind natürlich neben einem ausreichenden Vakuum, dass für Turbolenzen in der Milchleitung, also für die mechanische Reinigungskraft, zuständig ist, auch weitere Kriterien für eine gute Milchqualität einzuhalten. Dazu gehören neben anderem die Temperatur, die Zeit und das Reinigungsmittel. Grundsätzlich lassen sich zwei Spülungsvarianten unterscheiden, deren Elektroenergiebedarf aber kaum unterschiedlich ist: bei einer Zirkulationsreinigung wird für eine relativ kurze Zeit ein hoher Anschlusswert benötigt, die Kochendwasserreinigung heizt das Spülwasser über einen längeren Zeitraum mit einem geringeren Anschlusswert auf. Eine sogenannte Stapelreinigung nutzt das Nachspülwasser des vorangegangenen Spülvorgangs zum Vorspülen für die aktuelle Reinigung und hilft so Spülwasser einzusparen.
Bei der Planung einer entsprechenden betriebsangepassten Melkanlage sollte darauf geachtet werden, dass die Spültechnik und der Durchmesser sowie die Länge der Milchleitung richtig dimensioniert sind, zusätzlich könnte über eine Dämmung der Milchleitung nachgedacht werden um Wärmeverluste zu reduzieren. Melkstände, in denen Pokale zur Milchmengenmessung eingesetzt werden, haben durch die großen Volumina der Pokale einen höheren Wasser- und Heizenergiebedarf. Um warmes Wasser für die Spülung zu erzeugen, sollte über Alternativen zu Strom nachgedacht werden, da Heizen per Strom häufig das teuerste Verfahren ist. Eine Wärmerückgewinnung erzeugt z.B. je Liter Milch 0,6 Liter Wasser mit einer Temperatur von ca. 55 °C. Dieses Wasser kann je nach anfallender Menge im Stall zur Handwäsche, Kälbertränke, Melkstandreinigung oder Brauchwasser im Haushalt genutzt werden. Zur Melkstandreinigung muss dann nur noch die Differenz zwischen Wassertemperatur und Zielspülwassertemperatur z.B. mit Strom erhitzt werden.
Je nach aktuellen Preisen und der Betriebsstruktur können auch andere Heizalternativen eingesetzt werden. Dies sind z.B. Gas, Heizöl, Holz, Abwärme aus der Biogasanlage und andere. Zusätzlich zur Melkanlage muss auch der Milchtank gespült werden. Auch hier gilt in erster Linie, dass das Volumen des Tanks an die zu lagernde Milchmenge angepasst ist. Pro 100 Liter Tankvolumen werden etwa 1,5 Liter Wasser benötigt, eine Überdimensionierung verursacht also unnötigen Verbrauch an Wasser, Wärme, Zeit und Reinigungsmittel. Um die Funktion von Melkanlagen- und Tankreinigung sicherzustellen, sind die Anlagen regelmäßig zu warten, auch die Warmwassermenge und -Temperatur sollte regelmäßig geprüft und an Sollwerte angepasst werden.
Zur Milchkühlung werden entweder die Direktkühlung oder eine indirekte Kühlung mittels Eiswasser genutzt. Die Direktkühlung hat einen relativ hohen Wirkungsgrad, allerdings auch einen höheren Leistungsbedarf. Der Stromverbrauch wird mit ca. 2 kWh / 100 Liter Milch angegeben, was allerdings je nach Tank, Technik und Milchmenge unterschiedlich ist. Bei der Eiswasserkühlung wird über einen längeren Zeitraum Eis erzeugt und damit eine indirekte Kühlung der Milch bewirkt. Der Wirkungsgrad ist im Vergleich zur Direktkühlung geringer und der Stromverbrauch mit ca. 2,4 kWh / 100 Liter Milch höher.
Vor dem Hintergrund Strom und somit Kosten einzusparen und im Hinblick auf eine gute Milchqualität ist der Einsatz von Vorkühlern ab einer Jahresmilchmenge von etwa 250.000 kg sinnvoll, wie aus der Tabelle 4 ersichtlich wird.
Tabelle 4: Auswirkung von Vorkühlern auf die Kosten für Milchkühlung am Beispiel eines 2 x 7 Fischgrätmelkstands. (Quelle: Alfons Fübbeker, LWK NS)
Milchmenge pro Jahr | 250.000 kg | 500.000 kg | 750.000 kg |
---|---|---|---|
Anschaffungspreis | 2.500 € | ||
Kosten pro Jahr (Afa, Zinsen, Wartung) | 400 € | ||
Nutzen pro Jahr (50 % Stromeinsparung) |
2.500 kWh 500 € |
5.000 kWh 1.000 € |
7.500 kWh 1.500 € |
Kosteneinsparung pro Jahr | + 100 € | + 600 € | + 1.100 € |
Strombedarf für die Kühlung: Ø 2,0 kWh / 100 l Milch Strompreis: 20 ct / kWh |
Zur Milchvorkühlung werden Platten- oder Rohrkühler genutzt, die im Gegenstromprinzip mit Leitungs- oder Brunnenwasser arbeiten. Die Leistung eines Plattenkühlers kann durch die Anzahl der Platten angepasst werden, Rohrkühler haben nur eine Baugröße, können aber in Reihe geschaltet werden.
Durch Einsatz eines Vorkühlers kann der Strombedarf zur Milchkühlung um bis zu 50 % reduziert werden. Der Abkühleffekt ist abhängig von der eingesetzten Technik, von der Wassermenge je Liter Milch und natürlich von der Wassertemperatur. Brunnen- oder Stadtwasser haben eine Temperatur von etwa acht bis zwölf °C, die Milch erreicht den Vorkühler mit einer Temperatur von 33 bis 34 °C, beim Einsatz von 1 Liter Wasser je Liter Milch kann die Milch um etwa 15 bis 17 °C abgekühlt werden. Werden eine größere Wassermenge oder kälteres Wasser eingesetzt ist sogar eine Milchkühlung je nach Technik auf bis zu vier bis sechs °C möglich.
Die Vorkühlung wirkt sich positiv auf den Keimgehalt der Milch aus, Milch, die bereits im Lagertank ist, wird weniger stark wieder erwärmt. Der Wirkungsgrad eines Plattenkühlers kann mit einer Frequenzsteuerung für die Milchpumpe erhöht werden, da die Kühlwirkung bei gleichmäßigem Milchfluss besser ist. Dies ist besonders bei größeren Gruppenmelkständen interessant, weil dort in Intervallen große Milchmengen anfallen. Je nach Technik fallen ca. 1 bis 2 Liter lauwarmes Brauchwasser je gemolkenem Liter Milch an. Dieses Wasser kann in ausreichend dimensionierten Behältern gesammelt und in das Tränkesystem für Milchkühe und Jungvieh eingespeist werden. Im Hinblick auf die Wasserhygiene, sollten Lagerbehälter nicht transparent sein und nicht in der Sonne stehen, da durch Wärme und Licht das Wachstum unerwünschter Keime und Algen angeregt wird. Die Lagerbehälter sollten wenige Stunden nach dem Melken vollständig geleert sein und regelmäßig auf Verunreinigungen geprüft werden.
Die effiziente Arbeit der Kühlaggregate selbst sollte durch regelmäßige Wartung und Reinigung sichergestellt werden. Der Stromverbrauch der Kältemaschinen ist höher, je höher die Umgebungstemperatur ist, daher sollten die Aggregate eine gute Luftzufuhr haben und vor starker Sonneneinstrahlung geschützt werden. Die Aggregate lassen sich sehr gut außerhalb von Gebäuden installieren und benötigen nur eine einfache Beschattung (siehe Abbildung 7). Die Kühltechnik am Tank ist über die Jahre effizienter geworden, heute werden sogenannte Steppverdampfer genutzt, die Kühlkreisläufe können zusätzlich in verschiedene Ebenen eingeteilt werden um z.B. nur Teilbereiche des Lagertanks kühlen zu müssen. Auch bei der Kühlung sollte auf ein angepasstes Tankvolumen geachtet werden. Bei zweitägiger Milchabholung und ganzjähriger Abkalbung reichen in der Regel ca. 60 Liter Tankvolumen je Kuh aus. Eine andere Möglichkeit stellt die Nutzung von zwei Milchtanks für jeweils 2 Gemelke dar. Bei dieser Variante muss jeweils nur ein verhältnismäßig kleineres Volumen gekühlt werden, weil jeder Tank nach dem ersten Gemelk bereits zu 50 % gefüllt ist und nicht nur zu 25 % wie bei der Variante mit einem Tank für vier Gemelke. Diese Möglichkeit könnte eventuell für wachsende Betriebe sinnvoll sein.
Stromkosten reduzieren über Lastmanagement
Die Energieversorgung im Milchviehbetrieb ist nahezu ausschließlich auf Strom aufgebaut. Der Jahresstrombezug liegt bei der Mehrzahl unserer Milchkuhbetriebe unter 100.000 kWh bzw. in der Viertelstundenleistung unter 30 kW. Bis zu diesem Verbrauch wird ohne Leistungsmessung abgerechnet, daher ist ein Lastmanagement für solche Betriebe eher nicht von Bedeutung. Der Lastgang typischer Milchkuhbetriebe weist in der Regel zwei Spitzen auf, die durch die Melkzeiten hervorgerufen werden. Melkanlage, Milchkühlung und Spülung arbeiten fast gleichzeitig und verursachen einen hohen Leistungsbedarf. Für Betriebe, die die 30 kW Viertelstundenleistung überschreiten könnten, kann sich ein Lastmanagement rechnen.
Das Ziel ist es den Strombezug und die Leistungsabnahme zeitlich so abzustimmen, dass die Leistungskurve möglichst gleichmäßig verläuft und die Lastspitzen möglichst niedrig sind. Der Gesamtstromverbrauch wird dadurch nicht zwangsläufig gesenkt, allerdings ist ein gleichmäßiger Lastverlauf für den Kunden billiger. In sehr großen Milchviehanlagen und in Betrieben mit automatischem Melken ergibt sich fast automatisch ein günstigerer Lastverlauf, da nahezu fast rund um die Uhr gemolken und gekühlt wird. Mit Kochendwasserreinigung und indirekter Milchkühlung lassen sich Lastspitzen reduzieren, da die Anschlusswerte geringer sind und die Arbeit außerhalb der Melkzeiten stattfinden kann. Eventuell können die Arbeitsvorgänge auch in Schwachlastzeiten des Stromlieferanten, die sogenannte Niedertarifzeit gelegt und so noch weiter die Stromkosten gesenkt werden. Dieses gilt ebenfalls für weitere Stromabnehmer wie z.B. Güllerührer und Güllepumpe. Geräte mit hohen Anschlusswerten können mittels Zeitschaltuhr nacheinander geschaltet werden.
Alternativ ist eine sichere Maßnahme um Lastspitzen zu vermeiden die Verriegelung von Verbrauchern gegeneinander mit entsprechender Elektroinstallation. Mittels Computertechnik und festgelegten Schwellenwerten kann ebenfalls die Lastaufnahme geregelt und sichergestellt werden, dass die rechnungsrelevante Viertelstundenleistung nicht überschritten wird. Diese Maßnahmen setzen eine genaue Betriebanalyse der Abläufe und Zeiträume voraus. Diese allein kann schon sehr hilfreich sein um Einsparpotenziale aufzuzeigen und zu nutzen.
Fazit
Bei allen Einsparbemühungen muss gerade in der Milchproduktion immer sichergestellt sein, dass die Produktqualität sowie Tierschutz und Tiergesundheit erhalten bleiben. Je nach Betriebskonstellation lassen sich durch Verfahrensänderungen die Kosten für Energie beeinflussen. Die Einsparpotentiale in der Innenwirtschaft sind dabei von Betrieb zu Betrieb sehr unterschiedlich. Nicht immer muss dabei in teure Technik investiert werden, Abläufe neu zu organisieren und zu optimieren kann schon zu einem Erfolg führen.
Autorin, Fotos: Julia Glatz